Hot stamping foil is a versatile and popular material used in various industries including packaging, printing and product decoration. It adds a touch of elegance and sophistication to the products, making them stand out on the shelf. But have you ever wondered how this sparkling, eye-catching foil is made? In this article, we will explore the complex process of hot stamping foil manufacturing from raw materials to final product.
Before diving into the manufacturing process, it is necessary to understand what aluminum foil is. Hot stamping foil is a film coated with metallic or pigmented ink that can be transferred to a substrate such as paper, plastic or cardboard using heat and pressure. The result is a vibrant reflective finish that enhances the visual appeal of embossed items.
Raw materials
The production of hot stamping foil starts with the selection of raw materials. The main components include:
1.Base Film: Base film is usually made of polyester or other plastic materials. The film serves as a carrier for metallic or pigmented inks and provides the necessary strength and flexibility.
2. Metallic Pigments: These pigments are responsible for the gloss and reflective qualities of the foil. Common metallic pigments include aluminum, bronze and copper. The choice of pigment affects the final appearance of the foil.
3. Adhesive: Adhesives are used to bond metallic pigments to the base film. They ensure that the pigments adhere correctly during the stamping process.
4. Release Coating: Apply a release coating to aluminum foil to promote pigment transfer to the substrate. This coating enables the foil to easily separate from the base film during the stamping process.
5.Colored Inks: In addition to metallic pigments, colored inks can be added to create a variety of finishes, including matte, gloss, and satin.
You can please visit our this company product detail page, the model number is LQ-HFS Hot Stamping Foil for paper or plastic stamping
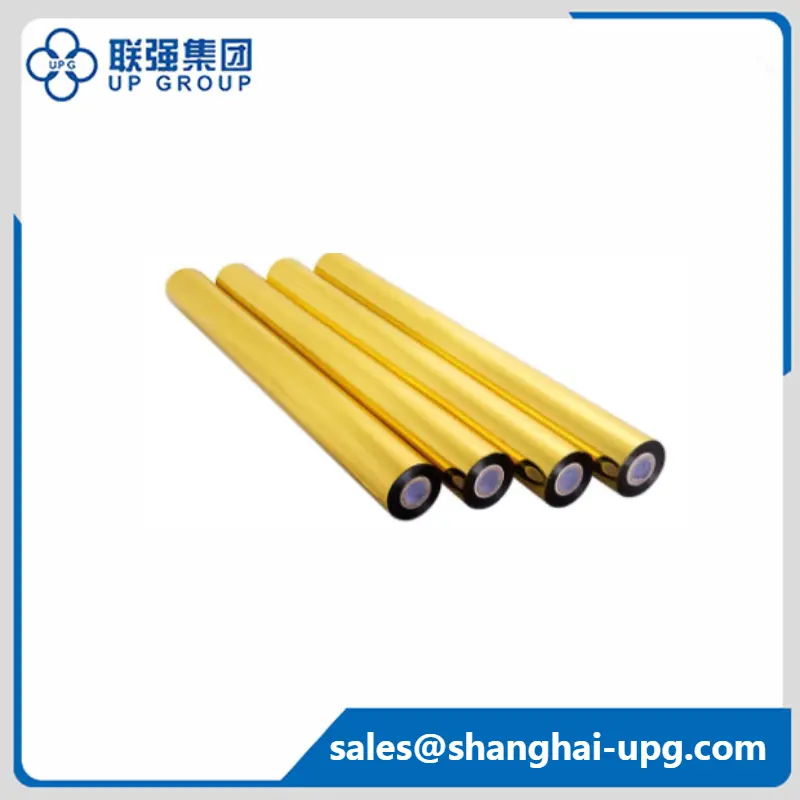
It is made by adding a layer of metal foil on the film base through coating and vacuum evaporation. The thickness of anodized aluminum is generally (12, 16, 18, 20) μ m. 500 ~ 1500mm wide.Hot stamping foil is made by coating release layer, color layer, vacuum aluminum and then coating film on the film, and finally rewinding the finished product.
Manufacturing Process
The production of hot stamping foil involves several key steps, each of which is critical to ensuring the quality and performance of the final product.
1. Film preparation
The first step in the manufacturing process is to prepare the base film. Polyester film is extruded into sheets, which are then treated to enhance their surface properties. This treatment improves ink and pigment adhesion during subsequent coating processes.
2. Coating
Once the base film is ready, the coating process begins. This involves applying a layer of adhesive to the film and then applying metallic pigments or colored inks. Coating can be done using various methods including gravure printing, flexographic printing or slot die coating.
The choice of coating method depends on the desired thickness and uniformity of the pigment layer. After application, the film is dried to remove excess moisture and ensure the adhesive sets properly.
3. Application of release coating
After applying metallic pigments and inks, an anti-stick coating is added to the film. This coating is crucial to the hot stamping process as it allows the pigment to transfer smoothly to the substrate without sticking to the base film.
4. Slitting and rewinding
Once the foil is coated and dried, it is cut into narrow rolls of the desired width. This process is essential to ensure that the foil can be fed easily into the foil stamping machine. After slitting, the foil is rewound into rolls, ready for distribution.
5. Quality Control
Quality control is an important part of the manufacturing process. Test foil samples for adhesion, color consistency and overall performance. This ensures the foil meets industry standards and customer expectations.
6. Packaging and Distribution
After passing quality control, the hot stamping foil will be packaged for distribution. It is critical to protect the foil from moisture and physical damage during shipping. Packaging often contains information about the foil's specifications, including its width, length and recommended applications.
Application of hot stamping foil
Hot stamping foil has a wide range of uses, including:
- Packaging: Many consumer products, such as cosmetics, food and beverages, utilize foil foil for branding and decoration.
- PRINTING: Hot stamping foil is commonly used in the printing industry to produce high quality labels, business cards and promotional materials.
- Product Decoration: Items such as greeting cards, gift wrap and stationery are often foil decorated to enhance their visual appeal.
- Security Features: Some hot stamping foils are designed with security features, making them ideal for use on banknotes, ID cards, and other sensitive documents.
The production of hot stamping foil is a complex and delicate process involving a variety of raw materials and manufacturing processes. From the selection of base film to the application of metallic pigments and anti-stick coatings, every step plays a vital role in producing high-quality foils that enhance the visual appeal of products across multiple industries. As consumer demand for eye-catching packaging decoration continues to grow, the importance of foil stamping in the market undoubtedly remains significant. Understanding how this extraordinary material is produced not only highlights its craftsmanship, but also its value in the world of design and branding.
Post time: Nov-04-2024